Rosie Nguyen / Vietnam Times
Aseptic filling technology provided by GEA Procomac helps manufacturers save energy and reduce carbon emissions during the product packaging process.
Net Zero has become a global focus in recent times as climate change increasingly impacts the planet. At COP26 (the 2021 United Nations Climate Change Conference), countries including Vietnam pledged to achieve net-zero emissions by 2050. Subsequently, many businesses and industries have taken concrete actions to align with this goal.
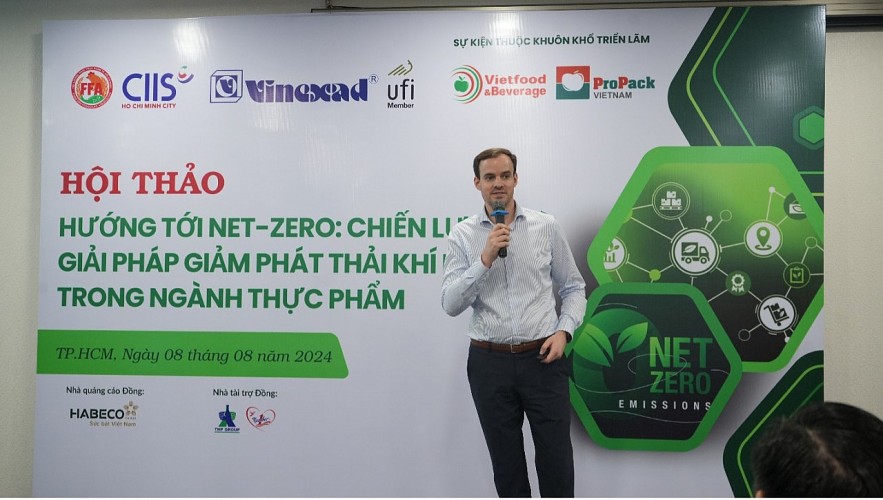
At the “Towards Net-Zero: Strategies and Solutions for Greenhouse Gas Reduction in the Food Industry” seminar held as part of the Vietfood & Beverage – Propack Vietnam 2024, leading organizations in the circular economy and green production in Vietnam shared their experiences and practical activities on the journey to Net Zero.
During the seminar, GEA Procomac, one of the world’s largest suppliers of process technology systems (machinery, plants, packaging) for the food, beverage, and pharmaceutical industries, shared insights into aseptic filling technology. This technology plays a strategic role in contributing to the company’s sustainability goals and achieving Net Zero by 2040, while providing sustainable solutions for many of GEA Procomac’s major partners worldwide, including Vietnam.
Filling is an indispensable step in any beverage production process, as it marks the completion of the product. Various filling methods such as hot, cold, and aseptic (room temperature sterilization) are currently employed in the global beverage industry.
Speaking at the seminar, Vincent Mauer, general director of GEA Vietnam and Philippines, explained that aseptic technology involves a complex series of interconnected processes (from processing, blending, UHT sterilization of the product, filling, and capping) to produce a finished product. The entire process takes place in a closed and sterile system. Both the bottle and the cap must be sterilized.
To minimize environmental impact, Aseptic filling systems can recover sterilization solutions for bottles and caps (Peracetic Acid – PAA) and reclaim sterile water, while also consuming less energy.
Vincent Mauer shared that GEA has been developing Aseptic technology since 1993 and has continuously improved it. This technology adheres to ISO 14021, focusing on saving space, water, and energy. The seventh-generation Aseptic line reduces water consumption by up to 91%, and cuts rinsing time in half compared to the previous generation. As a result, GEA’s customers can save up to 97,500 cubic meters of water annually, equivalent to the water usage of 2,100 people in a year.
“GEA is focused on minimizing the use of PET, as this is where we can make the biggest difference,” said Vincent Mauer. He stated that compared to hot filling technology, aseptic technology allows GEA’s customers to reduce greenhouse gas emissions by decreasing plastic usage and saving water. This means that manufacturers can optimize their consumption of both plastic and water.
Citing the Vietnamese market as an example, Mauer mentioned that Tan Hiep Phat, a pioneer in investing in Aseptic lines for producing healthy beverages, has managed to reduce the weight of their bottles by 50% thanks to GEA’s seventh-generation filling system, from 27 grams to 13.5 grams. This equates to a 20% reduction in CO2 emissions per bottle. “This allows Tan Hiep Phat to achieve its sustainability goals,” Vincent Mauer said.
Additionally, thanks to aseptic filling and capping at ambient temperature, Aseptic technology also reduces the need for energy consumption. The UHT sterilization process utilizes environmentally friendly technology and can recover heat, saving up to 90% of energy, compared to only 60% heat recovery in hot filling processes.
Furthermore, while products exposed to high temperatures for extended periods may experience a decline in quality and sensory attributes, Aseptic technology helps preserve the flavor, sensory qualities, and nutritional value of products. Aseptic technology is suitable for products that are difficult to preserve. Aseptically processed products can be stored at room temperature for up to 18 months without refrigeration. This method eliminates the need for preservatives in products, aligning with consumers’ current demand for natural, and organic beverages.
Tan Hiep Phat is currently the pioneering and sole partner in Vietnam to invest in 10 high-speed aseptic production and filling lines from GEA, located in factories across Vietnam. Tan Hiep Phat’s products are not only favored by domestic consumers but are also exported to over 20 international markets, including demanding markets such as the US, Japan, and South Korea, and are certified by the US Food and Drug Administration (FDA), and Halal standards for Islamic countries.
GEA Vietnam’s General Director revealed that Tan Hiep Phat is currently the largest customer utilizing GEA’s aseptic lines in Southeast Asia (SEAP). “GEA is delighted to be a strategic partner of Tan Hiep Phat, and contribute to the company’s sustainable development and continued success,” said Vincent Mauer.
At the seminar, Le Vinh Chuong, head of Research and Development at Tan Hiep Phat, shared that the company is committed to green production, from selecting leading environmentally friendly technologies to operating production processes that minimize the consumption of natural resources such as energy and water. “We believe that through our partnership with GEA, Tan Hiep Phat will achieve this goal,” said Chuong.
Source: https://vietnamtimes.org.vn/progressing-towards-net-zero-with-aseptic-filling-technology-76227.html